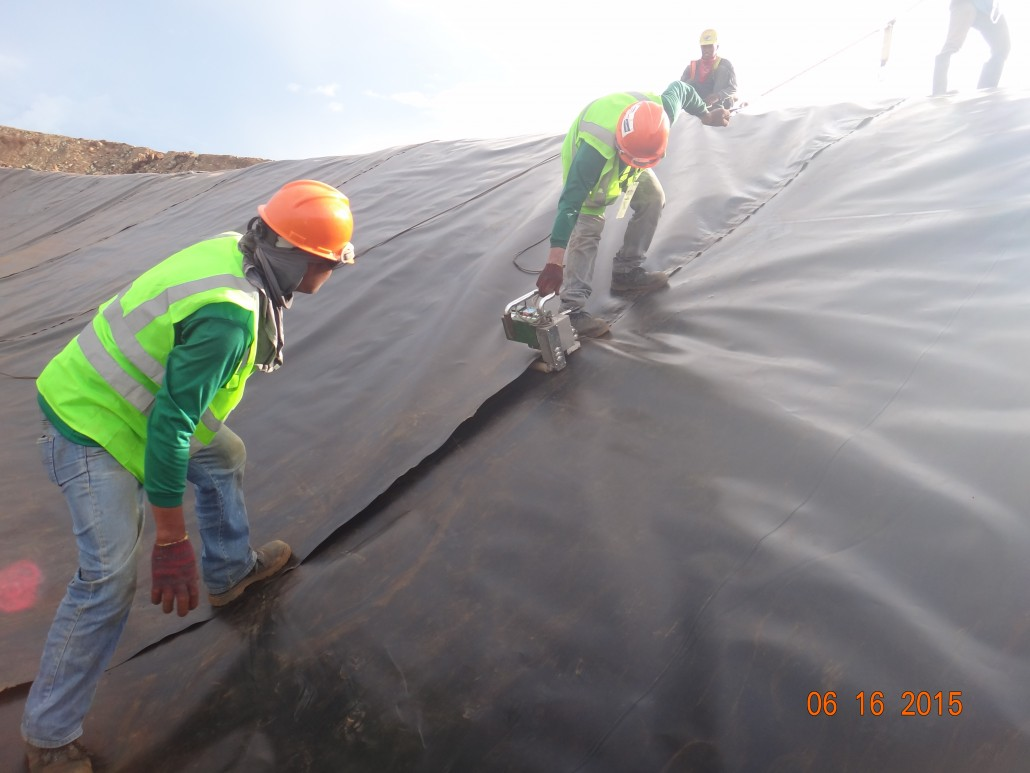
Composite geomembrane is a member of a large class of geosynthetic materials. Widely used in road, railway, water conservancy, large construction, power plant gray dam construction, non-ferrous metal tailings treatment, environmental protection engineering, soil and water conservation and other fields.
The service life of composite geomembrane mainly depends on whether the plastic film loses its impermeability and water resistance. According to national standards, 0.2 cm thick polyethylene film and stabilizer are used in water conservancy projects under clean water conditions. The service life can reach 40 ~ 50 years, and the service life under sewage conditions is 30 ~ 40 years. Therefore, the service life of the composite geomembrane is enough to meet the requirements of dam seepage prevention.
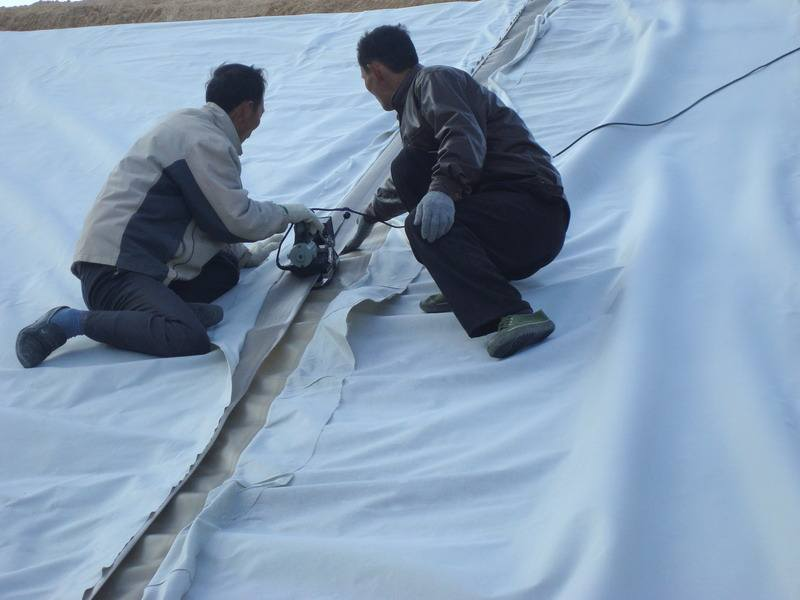
First, composite geomembrane product varieties: one geotextile belt with a geomembrane, two geotextile belts with a geomembrane, multiple geotextile belts with multiple geomembranes, and so on.
Second, composite geomembrane product features: integrated seepage and drainage, high strength, large friction coefficient, puncture resistance, aging resistance, acid and alkali resistance, and prevent soil erosion.
Third, the structure of composite geomembrane: composite geomembrane is to attach geotextile to one or both sides of the geomembrane to form a composite geomembrane. Its form consists of one geotextile and one geomembrane, two geotextiles and one geomembrane, two geomembranes and one geotextile.
Geotextiles are used as a protective layer for geomembranes to protect impermeable layers from damage. In order to reduce UV radiation and improve anti-aging performance, it is best to use the embedding method.
In construction, sand or clay with a smaller material diameter should be used first to level the foundation surface, and then the geomembrane should be laid. Geomembrane should not be stretched too tightly. The soil buried at both ends is partially corrugated. Finally, a layer of fine sand or clay is used on the laid geomembrane, with a thickness of 10 cm. Lay a 20-30 cm stone (or precast concrete block) for impact protection. During the construction process, every effort should be made to prevent the stone from directly impacting the geomembrane, and it is best to construct a protective layer when laying the membrane. The connection between the composite geomembrae and the surrounding structure should be anchored using expansion bolts and steel batons, and the connection part should be coated with emulsified asphalt (2mm thick) to prevent leakage.
Four, composite geomembrane construction precautions:
(1) Must be embedded: the thickness of the lid should not be less than 30 cm.
(2) The modified anti-seepage system shall include: buffer layer, anti-seepage layer, transition layer and protective layer.
(3) The soil should be firm, avoid uneven settlement, cracks, and should be cleared of turf and roots in impervious areas. Spread a small diameter of sand or clay on the surface in contact with the membrane as a protective layer.
(4) When laying, the geomembrane should not be pulled too tightly. It is best to bury the ends of the soil in a corrugated shape. Especially when using rigid materials for anchoring, a certain degree of expansion and contraction should be retained.
(5) During the construction process, stones and heavy objects should be avoided directly impacting the geomembrae. It is best to place the film at the same time as covering the film and cover the film with a protective layer.
Fifth, joint of composite geomembrane:
Joint treatment of composite geomembrane is the key process, which directly affects the anti-seepage effect. The general joint methods are: ① lap: the width of the lap should be greater than 15cm; ② Hot welding: suitable for thicker geomemofilm substrate, joint lap width is not less than 5CM. (Glue is not recommended, it is easy to unglue after long-term immersion in water, and the anti-seepage effect is poor.)
Sixth, composite geomembrane joint precautions:
(1) The combined treatment of composite geomembrane is a key step in construction and directly affects the service life of the project. According to the quality check, it is ideal to use hot welding. (It can also be bonded with special glue) The heating welding method is to heat treat the surface of the PE geomembrane, melt it, and then fuse it into one through pressure.
(2) Geomembrane is best laid in a certain direction. Both sides of the geomembrane have a certain PE film and PET non-bonding layer. When laying, the geomembrane direction of each unit should be adjusted to facilitate the welding of the geomembrane of the two units. ,
(3) After laying the geomembrane, apply sandbag pressure to windproof, and the edge joints should be free of dust, moisture, dust, etc.
(4) Before welding, adjust the PE single-layer film on both sides of the joint so that it overlaps with a certain broadband and is flat and wrinkle-free.
(5) When welding, it is best to weld by technicians with certain experience. Welding is done by special welding machines. Adjust the temperature and speed.